Sie sind voller Energie und möchten am liebsten sofort mit Ihrer Geschäftsidee ein Start-up gründen? Dann sollten Sie sich besser ein wenig ausbremsen und zuerst eine Unternehmensstrategie entwickeln. Was genau das ist, welche Strategien es gibt und was dabei zu beachten ist, erfahren Sie hier.
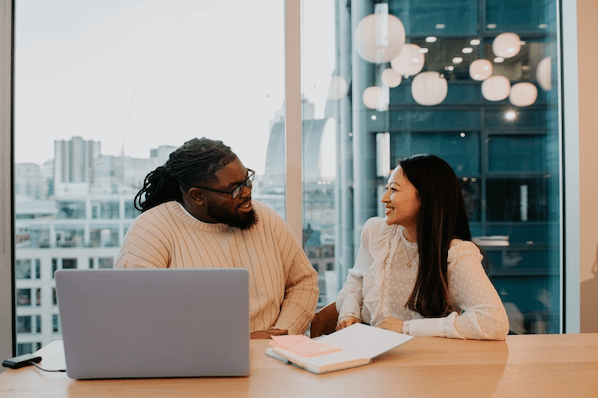
Was ist eine Unternehmensstrategie?
Eine Unternehmensstrategie, im Englischen „Corporate Strategy“ genannt, ist ein Plan, mit dem ein Unternehmen seine langfristigen Ziele definiert. Aus dieser Strategie werden zahlreiche Maßnahmen abgeleitet, die sich auf alle Abteilungen und Mitarbeitenden auswirken.
Was wird in der Unternehmensstrategie festgelegt?
Mit einer Unternehmensstrategie halten Sie die Vision und Mission Ihres unternehmerischen Vorhabens fest. Dazu gehören unter anderem die Definition Ihrer Unternehmensziele auf Basis von Marktanalysen sowie die Festlegung der Zielgruppen, der Positionierung und des Produktportfolios. Auch die Ausarbeitung des Kundennutzens und die Formulierung einer Wettbewerbsstrategie stellen einen wichtigen Teil dar.
Das bedeutet, Sie klären mit Ihrer Unternehmensstrategie, womit Ihr Unternehmen in welchen Märkten, mit welchen Produkten und welchen Maßnahmen erfolgreich sein möchte. Dafür sollten Sie Ziele und Meilensteine erarbeiten, ergänzt um relevante Kennzahlen. Nur so ist es Ihnen möglich, die Entwicklung Ihres Vorhabens zu bewerten.
Warum ist eine Unternehmensstrategie wichtig?
Eine Unternehmensstrategie ist von zentraler Bedeutung, um den langfristigen Erfolg Ihres Unternehmens zu sichern. Als Unternehmer oder Unternehmerin sollten Sie nie aus dem Bauch heraus Entscheidungen treffen. Stattdessen ist es ratsam, eine Strategie zu verfolgen. Ihre Unternehmensstrategie gibt Ihnen Orientierung und hilft dabei, den Fokus auf das Wesentliche zu lenken. Mithilfe einer Unternehmensstrategie können Sie:
- Langfristige Ziele verfolgen: Mit einer klaren Strategie können Sie sich auf Ihre langfristigen Ziele konzentrieren und sicherstellen, dass alle Ihre Handlungen und Entscheidungen auf diese Ziele ausgerichtet sind.
- Entscheidungsfindung erleichtern: Eine festgelegte Strategie bietet einen Rahmen, der Ihnen hilft, fundierte Entscheidungen zu treffen, anstatt impulsiv oder ad hoc zu handeln.
- Anpassungsfähigkeit: Die Geschäftswelt ist dynamisch. Führt Ihre Unternehmensstrategie nicht dazu, Ihre Ziele effektiv zu erreichen? Dann sollten Sie Ihre Prozesse und Maßnahmen anpassen. Mit einer soliden Strategie können Sie besser auf Marktveränderungen reagieren und Chancen nutzen, wenn sie sich ergeben.
- Ressourcenoptimierung: Eine Strategie ermöglicht es Ihnen, Ihre Ressourcen effizient zu nutzen und sicherzustellen, dass Sie Ihre Zeit, Ihr Geld und Ihre Energie in die richtigen Projekte und Initiativen investieren.
Sind Sie ein Gründer oder eine Gründerin? Dann dient die Unternehmensstrategie dazu, Ihren Businessplan zu erfüllen. Dieser stellt die Basis für die Strategie Ihres Unternehmens dar. Weichen Sie zu sehr von den ursprünglichen Planungen ab, verärgert das unter Umständen Banken sowie Investoren und Investorinnen. Denn diese haben Ihnen auf Basis Ihres Businessplans, in dem Sie Ihre Unternehmensstrategie festgehalten haben, Kredite gewährt oder Investitionen getätigt.
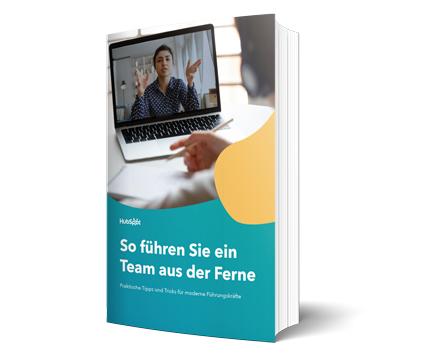
Remote Leadership: So führen Sie ein Team aus der Ferne
Wir verraten, was das für Führungskräfte bedeutet und mit welchen Tipps & Tricks Sie Ihr Team auch aus der Ferne erfolgreich führen.
- Der Unterschied: Vor Ort und aus der Ferne
- Welche Führungsstile eignen sich?
- Das A & O: Virtuelle Strukturen
- 7 praktische Tipps für den Alltag als Führungskraft aus der Ferne
Was gibt es für Unternehmensstrategien?
Es gibt verschiedene Unternehmensstrategien, die sich bewährt haben. Eine Strategie ist die sogenannte Kostenführerschaft, bei der Sie Ihre Angebote zu möglichst niedrigen Preisen anbieten. Alternativ können Sie eine spezielle Positionierung verfolgen, beispielsweise in einer Nische oder durch eine deutliche Differenzierung zum Markt.
Nachdem Sie nun einen Überblick über die verschiedenen Strategieoptionen haben, lassen Sie uns diese näher betrachten und erläutern, wie sie in der Praxis umgesetzt werden können.
Kostenführerschaft
Bei dieser Strategie bieten Sie Ihre Produkte oder Dienstleistungen zu den niedrigsten Kosten im Vergleich zu Ihren Wettbewerbern an. Die ist möglich, indem Sie Skaleneffekte nutzen, Produktionsprozesse optimieren oder in großen Mengen einkaufen. So können Sie sich einen Vorteil verschaffen und einen größeren Marktanteil gewinnen.
Nischenstrategie
Hier konzentrieren Sie sich auf ein spezifisches Marktsegment oder eine Zielgruppe. Vielleicht gibt es eine Nische, die von den großen Playern übersehen wird? Indem Sie sich auf diese Marktlücke spezialisieren, können Sie die spezifischen Bedürfnisse Ihrer Kundschaft besser erfüllen.
Differenzierung
Bei dieser Strategie haben Sie die Chance, sich durch besondere Produkteigenschaften, ein einzigartiges Markenimage oder herausragenden Kundenservice von der Konkurrenz abzuheben. Wichtig ist, dass Sie einen Mehrwert für Ihre Kunden und Kundinnen schaffen.
Jede dieser Strategien bietet Ihnen besondere Chancen. Überlegen Sie sorgfältig, welche am besten zu Ihnen und Ihrem Unternehmen passt, und nutzen Sie die Gelegenheit, sich auf dem Markt zu etablieren.
Unternehmensstrategie: Ein Beispiel
Um Ihnen das Thema anschaulicher zu vermitteln, schauen wir uns die Unternehmensstrategie am Beispiel von Apple an. Das Unternehmen hat sich auf Premiumprodukte spezialisiert, die ein exzellentes Nutzererlebnis bieten. So war das iPhone nicht das erste Smartphone der Welt, aber das erste mit einer intuitiven und einfachen Bedienung. Dafür wurden Features wie ein Flash Player Plug-in und eine haptische Tastatur gestrichen.
Noch heute verfolgt Apple das technische Motto „Reduce to the Max“. Zugleich besteht die Corporate Strategy des US-amerikanischen Unternehmens darin, sich an keinem Preiskampf zu beteiligen. Die Produkte gehören zu den teuersten in ihrem Segment, wodurch die Positionierung als Premiummarke unterstrichen wird.
Unternehmensstrategie entwickeln: So gehen Sie dabei vor
Die Entwicklung einer Unternehmensstrategie erfolgt in mehreren Schritten. Im Folgenden haben wir Ihnen die wichtigsten aufgelistet.
1. Markt- und Wettbewerbssituation analysieren
Zunächst sollten Sie eine umfassende Marktanalyse durchführen, um die Ist-Situation einschätzen und eine Prognose zum Wachstumspotenzial des Marktes tätigen zu können. Außerdem ist eine Konkurrenzanalyse sinnvoll, aus der sich Unterschiede zwischen Ihrem Unternehmen und den Wettbewerbern ergeben. Auf Basis dessen können Sie Ihr Alleinstellungsmerkmal (USP) definieren, das Ihr Unternehmen hervorhebt.
2. Ziele definieren
Ziele sind der Ausgangspunkt jeder Unternehmensstrategie. Es ist essenziell, klare Meilensteine und Zeitpunkte festzulegen, wie zum Beispiel das Erreichen des Break-even-Point im zweiten Geschäftsjahr oder das Erreichen einer bestimmten Umsatzgrenze. Diese Ziele bilden die Grundlage für alle weiteren strategischen Entscheidungen und Maßnahmen.
3. Identifikation der Zielgruppen
Es ist essenziell, dass Sie ein tiefgehendes Verständnis für Ihre (potenziellen) Zielgruppen entwickeln. Legen Sie fest, wer Ihre Kundschaft ist, welche Bedürfnisse sie haben und erarbeiten Sie einen eindeutigen Kundennutzen. Finden Sie heraus, auf welchem Weg Sie Ihre möglichen Kunden und Kundinnen effektiv ansprechen können.
4. Mission und Vision entwickeln
Legen Sie die grundlegenden Werte sowie die Vision Ihres Unternehmens fest. Während die Vision die zukünftige Ausrichtung skizziert, bestimmen die Unternehmenswerte und die Mission das alltägliche Verhalten und die Entscheidungsprozesse in Ihrem Unternehmen.
5. Strategische Optionen ausloten
Basierend auf der Analyse des Zielmarktes und seiner Marktgegebenheiten sollten Sie mehrere strategische Alternativen entwickeln. Diese Optionen helfen Ihnen dabei, Ihre strategischen Ziele zu erreichen.
6. Auswahl einer Strategie
Entscheiden Sie sich für die Strategie, die optimal zu Ihren Zielen, Ihrer Vision und Ihren Werten passt. Dies könnte zum Beispiel eine Unternehmensstrategie sein, die eine Kostenführerschaft oder eine Premium-Positionierung anstrebt.
Unternehmensstrategie vs. Geschäftsfeldstrategie: Was ist der Unterschied?
Eine Unternehmensstrategie definiert langfristige Ziele und die allgemeine Richtung, die ein Unternehmen einschlagen soll. Sie ist die übergeordnete Strategie, die auch den Rahmen für die verschiedenen Geschäftsfeldstrategien festlegt.
Geschäftsfeldstrategien beziehen sich auf bestimmte Segmente oder Abteilungen eines Unternehmens. Diese Strategien sind darauf ausgerichtet, in den jeweiligen Märkten oder Industrien erfolgreich zu sein. Sie sollten im Einklang mit der übergeordneten Unternehmensstrategie stehen.
Fazit: Mit der Corporate Strategy zum langfristigen Erfolg
Start-ups, aber auch etablierte Unternehmen vernachlässigen häufig ihre Unternehmensstrategie. Sie handeln entweder planlos oder verfolgen viele kleine Ziele, die nicht auf ein großes Überziel einzahlen. Solch ein Vorgehen kann erfolgreich sein. Im Laufe der Zeit steigt jedoch das Risiko, dass eine Firma oder Organisation langfristig scheitert.
Deshalb ist es wichtig, gleich zu Beginn eine Unternehmensstrategie zu entwickeln und diese konsequent zu verfolgen. Bei starken Veränderungen am Markt oder einer schweren Krise ist es zudem sinnvoll, die Strategie zu überdenken und den Gegebenheiten anzupassen.
Titelbild: Catherine Falls Commercial / iStock / Getty Images Plus