Ganz gleich, ob es sich um ein neues Produkt, die Vermarktung eines Produkts in neuen Märkten oder die Neuveröffentlichung eines Produkts handelt: Erfolgreiches Produktmarketing spielt eine wesentliche Rolle für den Markterfolg von Produkten und Dienstleistungen aller Art. Nicht nur im B2C-, sondern auch im B2B-Bereich ist es daher wichtig, die Mechanismen des Produktmarketings zu verstehen.
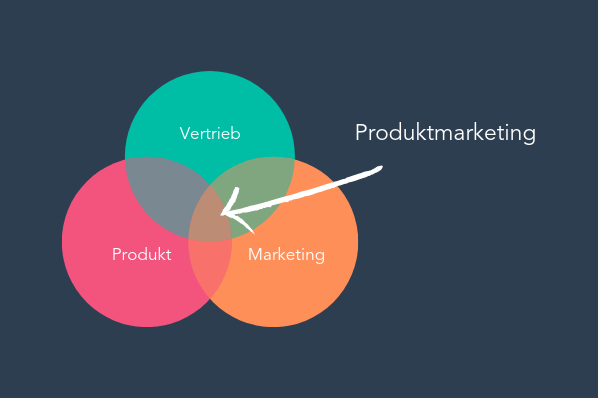
Worauf Sie beim Produktmarketing achten sollten, erfahren Sie hier.
Was ist „Produktmarketing“?
Das Produktmarketing umfasst alle Aktivitäten, die gezielt darauf ausgerichtet sind, Produkte kundenorientiert zu entwickeln und zu vermarkten. Damit bestimmt es maßgeblich den Markterfolg. In der Regel liegt die Verantwortung für das Produktmarketing bei einem Produktmanager, der ein Produkt über seine gesamte Lebensdauer hinweg betreut.
Die zentralen Aufgaben im Produktmarketing
Zu den zentralen Aufgaben eines Produktmanagers gehören die Bereiche Information, Planung, Kontrolle und Koordination. Im Produktmarketing sind Sie dazu angehalten, mit allen Abteilungen Ihres Unternehmens zu kooperieren, die für den Markterfolg eines Produktes relevant sind – zum Beispiel der Forschung und Entwicklung oder dem Einkauf. In Ihrer Rolle als Produktmanager schneiden Sie daher viele verschiedene Unternehmensbereiche an und arbeiten sowohl strategisch als auch operativ, weshalb sich ein Job im Produktmarketing recht abwechslungsreich gestaltet.
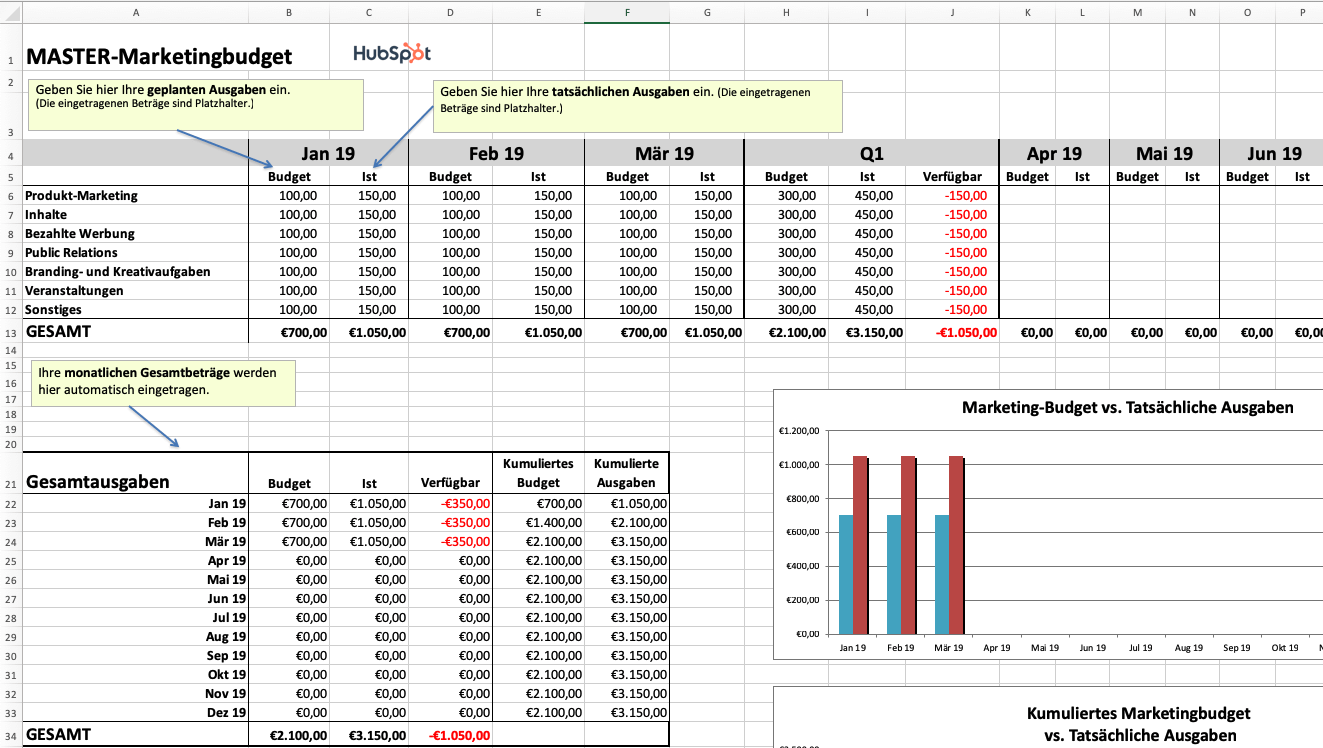
Vorlagen für die Verwaltung von Marketingbudgets
Mit diesen Budgetvorlagen für Microsoft Excel und Google Sheets können Sie Ihr Marketingbudget ganz einfach kontrollieren.
- Produkt-Marketing
- Bezahlte Werbung
- Website-Neugestaltung
- Events
Produktmarketing: Ein Plan für alle Phasen, die ein Produkt durchlebt
Als Anhaltspunkt, mit welchen Marketinginitiativen Sie sich im Produktmarketing zu welchem Zeitpunkt beschäftigen sollten, kann das Modell vom Produktlebenszyklus dienen: Es beschreibt alle Entwicklungsphasen eines Produkts – von der Markteinführung bis hin zum Marktaustritt.
Dieses theoretische Modell stellt in der Praxis klare Anforderungen an den jeweiligen Produktmanager: Seine Aufgabe ist es, das Produkt während der gesamten Lebensdauer auf dem Markt zu betreuen. Das Modell unterteilt diese Zeit in die fünf Phasen: „Einführung“, „Wachstum“, „Reife“, „Sättigung“ und „Degeneration“ (oder „Rückgang“).
Jede dieser einzelnen Phasen bringt unterschiedliche Aufgaben im Produktmarketing mit sich:
Einführung
Ihr Produkt ist entwickelt – nun müssen Sie es auf den Markt bringen! Die Veröffentlichung des Produkts stellt eine enorm spannende Aufgabe im Produktmarketing dar. Denn hier wird versucht, das Produkt bekannt zu machen und über den Vertrieb an potenzielle Kunden zu bringen. Die Marketingaktivitäten sollten sich darauf konzentrieren, mit intensiven Kommunikationsmaßnahmen die notwendige Reichweite in der entsprechenden Zielgruppe zu generieren. Dies gelingt Ihnen am besten mit einem geeigneten Mix aus Outbound-Marketing, also der klassischen, direkten Werbung, und Inbound-Marketing: Content-Marketing, Social-Media-Marketing und SEO.
Wachstum
Haben Sie das Produkt erfolgreich auf den Markt gebracht, sollte sich dieses dort auch zunehmend breiter platzieren, um Wettbewerber langfristig zu verdrängen. Zu den Aufgaben des Produktmanagers zählt es daher, neue Marktentwicklungen und Möglichkeiten früh zu erkennen. So können weitere Vertriebspartner und lohnenswerte Marketingaktivitäten zeitnah identifiziert und angegangen werden. Ziel ist es, die Verwendung des Produkts zu maximieren und die eigene Marktpenetration auszudehnen.
Reife
Wird der Markt reifer, steigt die Anzahl von Wettbewerbern und damit der Konkurrenzdruck entsprechend an. Dann müssen sich auch Ihre Marketingaktivitäten entsprechend verändern. Als Produktmanager liegen jetzt klassische Business-Development-Aufgaben vor Ihnen: Sie sollten sich auf den Aufbau von Produkt- bzw. Markentreue konzentrieren. Eine klare Positionierung, wofür Ihr Produkt oder Ihre Marke steht und wofür nicht, ist wichtig, um sich bei Ihrer Zielgruppe im Überangebot gegen andere Wettbewerber durchzusetzen und Ihre Kunden langfristig emotional an Ihr Produkt zu binden. Als Schnittstelle zwischen den relevanten Abteilungen in Ihrem Unternehmen betreuen Sie die Optimierung der Customer Journey für Ihre Kunden, damit diese vom ersten Kontakt und Kauf bis hin zum Service ein großartiges Produkterlebnis haben.
Sättigung
Gehen Umsatz und Gewinn aufgrund von Marktsättigung immer weiter zurück, müssen Sie neue Wege beschreiten. Beispielsweise durch die Neuveröffentlichung eines Produkts: Bieten Sie beispielsweise eine bestimmte Software an, kann diese überholt werden und, mit einem neuen Image versehen, frisches Interesse auf dem Markt wecken.
Degeneration / Rückgang
Sinken die Umsätze Ihres Produkts trotz Ihrer Bemühungen weiter, kann es schließlich dazu kommen, dass Sie keinen Gewinn mehr erwirtschaften und sich Verluste einstellen. Stehen Sie an diesem Punkt, so ist Ihr Einsatz auch in der letzten Phase, dem Marktaustritt, gefragt: Jetzt gilt es, das Produkt „abzumanagen“, es also abzusetzen und in diesem Zug Investitionen in das Produktmarketing einzustellen. Stattdessen lohnt es sich, sich auf die Entwicklung und Vermarktung eines Nachfolgeprodukts zu konzentrieren, für das wiederum ein Marktpotenzial besteht.
Produkteinführung: Die Vorbereitung ist ausschlaggebend für den Markterfolg
Gerade bei neuen Produkten ist es wichtig, das Produktmarketing frühzeitig zu starten. Die Phase der Produkteinführung ist vor allem für Start-ups ausschlaggebend, denn sie kann über den Markterfolg eines neuen Produkts – und damit den Erfolg des jungen Unternehmens – entscheiden. Dies misslingt, wenn sich Start-ups zu stark auf die Entwicklung eines neuen Produkts fokussieren und die Marktvorbereitung dabei aus den Augen verlieren. Eine eindeutige Go-to-Market-Strategie im Produktmarketing ist also mindestens genauso wichtig wie ein gutes Produkt.
Ein gelungenes Produktmarketing beinhaltet daher schon lange vor der Produkteinführung umfassende Analysen: Dazu zählt beispielsweise, das Alleinstellungsmerkmal Ihres Produkts, also den USP (Unique Selling Point), zu identifizieren und klar herauszustellen, den Produktnutzen für Ihre potenzielle Zielgruppe herauszufinden und eine geeignete Preisgestaltung festzulegen.
Auch eine umfassende Marktanalyse, bei der Informationen zu den Wettbewerbern und der jeweiligen Zielgruppe gesammelt werden, ist wichtig, um ideal auf eine Produkteinführung vorbereitet zu sein. Dabei lohnt es sich, Methoden wie die SWOT-Analyse heranzuziehen, mit der interne Stärken und Schwächen analysiert und externe Chancen und Risiken ermittelt werden können. Je präziser und sorgfältiger Sie Ihr Produkt und den Markt analysieren, desto einfacher wird es Ihnen gelingen, geeignete Vermarktungsstrategien zu entwickeln.
Voraussetzung für erfolgreiches Produktmarketing: Den Überblick behalten
Nur durch ein kontinuierliches Beobachten von neuen Entwicklungen und Trends können Sie am Puls der Zeit bleiben. In Zeiten von Globalisierung und Digitalisierung ist dies von zunehmender Bedeutung, da Märkte und Zielgruppen immer rascher erschlossen werden können. Dadurch sehen sich sowohl Marketing als auch Vertrieb entsprechend mit großen Herausforderungen konfrontiert und müssen schnell reagieren.
Weil das Produktmarketing so vielfältige Aufgaben mit sich bringt, ist es außerdem enorm wichtig, stets den Überblick über die unterschiedlichen Anforderungen zu behalten. Zum Glück gibt es Tools, die Ihnen im Produktmanagement bei der Organisation der einzelnen Bereiche helfen. Trello etwa erleichtert die Zusammenarbeit mit den relevanten Abteilungen Ihres Unternehmens und vereinfacht die Koordination von Aufgaben, während das kostenlose HubSpot CRM Ihnen dabei hilft, die verschiedenen Aufgaben und Prioritäten in den einzelnen Phasen des Produktlebenszyklus zu managen, Vertriebsaufgaben zu automatisieren und mögliche Geschäftsabschlüsse transparent nachzuverfolgen.
Konkrete Hilfestellungen finden Sie außerdem in dieser Liste von Product Hunt mit über 300 kostenlosen Vorlagen für beliebte Produktmanagement-Softwaretools wie G-Suite, Trello oder Airtable, die praktischerweise in Kategorien wie „Strategie“, „Planung“ oder „Research“ gegliedert sind.
Der Erfolg eines Produkts ist eng mit einem gelungenen Produktmarketing verknüpft. Daher sollte die umfangreiche Arbeit des Produktmarketings bereits vor der Produkteinführung beginnen, um das Produkt später optimal am Markt platzieren zu können. Mit den aufgezeigten Entwicklungen, die Sie im Produktmarketing während der einzelnen Phasen des Produktlebenszyklus beobachten (und natürlich auch entsprechend darauf reagieren) sollten, sowie den verschiedenen Tools, die Ihnen diese Aufgaben erleichtern, sind Sie mit einem Set an Werkzeugen ausgestattet, mit dem Sie Ihr Produktmarketing bestmöglich steuern können.