Damit anstehende Projekte erfolgreich geplant und durchgeführt werden können, ist eine strukturierte Arbeitsweise elementar. In der Praxis haben sich verschiedene Methoden zur Organisation eines Projekts etabliert. Eine davon: der Projektstrukturplan.

Im folgenden Artikel erfahren Sie, was ein Projektstrukturplan ist und wie Sie Ihren eigenen Plan für eine gesteigerte Organisation und Produktivität erstellen können.
Was ist ein Projektstrukturplan?
Ein Projektstrukturplan (PSP) führt alle inhaltlichen Elemente und Arbeitspakete eines Projektes in hierarchischer Abfolge auf. Der Plan ist meist in einer Baumstruktur dargestellt und gliedert ein übergeordnetes Projekt in Teilprojekte, Teilaufgaben und einzelne Arbeitspakete. Dabei spielt die zeitliche Komponente keine Rolle.
Warum wird ein Projektstrukturplan erstellt?
Komplexe Projekte erfordern eine detaillierte Planung. Ohne klare Struktur für die anfallenden Aufgaben drohen vor allem arbeitsreiche Projekte, in die viele Personen involviert sind, ineffizient zu werden. Damit alle Beteiligten durchgehend einen Überblick über die Projektaufgaben und ihre Abhängigkeiten haben, wird ein PSP eingesetzt.
Wann wird der Projektstrukturplan erstellt?
Der Projektstrukturplan steht am Anfang der Planung eines Projekts und hilft Projektleitern und Projektleiterinnen im späteren Verlauf, jederzeit den Überblick zu wahren. Ehe das Projekt beginnt, muss der PSP stehen.
Die unterschiedlichen Ansätze für Ihren Projektstrukturplan
Der in der Praxis auch WBS (Work Breakdown Structure) genannte Projektstrukturplan folgt zwar einer klaren Logik, unterliegt aber keiner Norm oder einem einheitlichen Standard. Unter Projektverantwortlichen werden daher in der Regel drei Arten des Projektstrukturplans unterschieden:
- Phasenorientierter Projektstrukturplan
- Funktionsorientierter Projektstrukturplan
- Objektorientierter Projektstrukturplan
In ihren Grundsätzen sind die drei Orientierungen gleich — das Projekt wird jeweils vom Großen ins Kleine strukturiert. Die kleinste Einheit sind dabei immer die Arbeitspakete. Welcher Ansatz für Sie am besten geeignet ist, hängt von Ihren individuellen Anforderungen ab.
Phasenorientierter Projektstrukturplan
Gerade bei Entwicklungsprojekten finden Sie in der Praxis oft einen phasenorientierten Projektstrukturplan vor. Dabei werden einzelne Phasen auf der höheren Ebene definiert, die durchlaufen werden müssen.
Das können beispielsweise bei einem Bauprojekt Standortplanung, Entwurf, Bau, Inbetriebnahme und Verwaltung sein. Bevor eine Phase mit ihren Teilaufgaben und Arbeitspaketen nicht abgeschlossen ist, kann die nächste im Regelfall noch nicht bearbeitet werden.
Funktionsorientierter Projektstrukturplan
Beim funktionsorientierten Projektstrukturplan hingegen orientieren sich die einzelnen Hierarchien auf der höchsten Ebene an den Funktionsbereichen Ihres Unternehmens. Diese können beispielsweise Vertrieb, Marketing, Produktion und Buchhaltung lauten.
Der Vorteil dieses Ansatzes liegt darin, dass Kollegen und Kolleginnen die Struktur bereits aus dem Arbeitsalltag und Organigrammen kennen. Dadurch wird kein ausführliches Briefing benötigt, wer wofür zuständig ist und an wen berichtet.
Eine abgewandelte Form des funktionsorientierten Projektstrukturplans ist der aktivitätsorientierte Plan. Dabei sind die anfallenden Tätigkeiten auf höheren Ebenen des Baumdiagramms bereits konkreter aufgeführt.
Ein Projektstrukturplan kann auch objektorientiert sein
Die beiden genannten Orientierungen gehen jeweils nicht vom Endprodukt aus. Ein objektorientierter Projektstrukturplan hingegen unterteilt das Projekt beziehungsweise Produkt in seine Einzelteile und organisiert so die anfallenden Arbeitspakete.
Ist Ihr anstehendes Projekt beispielsweise die Organisation eines Musikfestivals mit mehreren Bühnen, so wären mögliche Teilprojekte in einem objektorientierten PSP die verschiedenen Bühnen, der Einlassbereich, das Cateringzelt und der Sanitärbereich.
Was gehört in einen Projektstrukturplan?
Für den Aufbau eines Projektstrukturplans gibt es verschiedene Ansätze und Methoden, die sich in der Praxis etabliert haben. Losgelöst vom gewählten Ansatz enthält ein PSP stets das betreffende Projekt, einzelne Teilprojekte, Teilaufgaben sowie Arbeitspakete. Die einzelnen Arbeitspakete werden — idealerweise von den Verantwortlichen selbst — ausführlich beschrieben.
So geht’s: Projektstrukturplan erstellen
In der Realität müssen Sie nicht zwingend eine der drei genannten Orientierungsformen wählen. Mischpläne sind durchaus üblich und können je nach Anforderung Ihres Projekts sinnvoll sein. Damit bei der Erstellung Ihres PSP nichts schiefgeht, gilt es, einige Eckpunkte zu beachten.
Projektstrukturplan: Der richtige Aufbau
Bevor Sie sich in die Ausgestaltung Ihres Projektstrukturplans stürzen, sollten Sie die Orientierungsform und anschließend das Schema für Ihren Plan wählen. Es gibt drei Möglichkeiten:
- Top-down: Sie legen zuerst die oberen Ebenen fest und arbeiten sich dann hierarchisch nach unten. Der letzte Schritt ist die Ausarbeitung der Arbeitspakete.
- Bottom-up: Dieser Ansatz ist das Gegenteil zum Top-down-Vorgehen. Sie erfassen im ersten Schritt alle kleinen Arbeitspakete und arbeiten sich so bis zu den Teilprojekten hierarchisch nach oben.
- Jojo: Die dritte Möglichkeit ist eine Mischform. Sie verbinden beide Methoden, legen beispielsweise nur die oberste Ebene fest und arbeiten dann Arbeitspakete aus. So entsteht im Zusammenspiel Ihr PSP.
Unabhängig vom gewählten Schema verknüpfen Sie im nächsten Schritt die Aufgaben mit den einzelnen Ebenen und ordnen alle ermittelten Tätigkeiten und Schritte zu.
Danach codieren Sie den gesamten Plan, damit alle Beteiligten damit arbeiten können. Dies kann numerisch, alphabetisch oder alphanumerisch erfolgen. Die oberste Ebene ist beispielsweise mit A, B, C und D deklariert, die einzelnen Teilaufgaben mit A1, A2, B1, B2 und so weiter. Diese Codierung führen Sie bis auf die unterste Ebene fort.
Als Hilfsmittel zur Erstellung Ihres Projektstrukturplans können Sie Online-Tools oder eine spezielle Software verwenden.
Die Arbeitspakete
Die unterste Ebene bilden in jedem Projektstrukturplan die einzelnen Arbeitspakete. Sie sind die kleinste Einheit und in der operativen Tätigkeit konkrete Aufgaben, die von den Projektbeteiligten erledigt werden müssen.
Sie sind selbst nicht weiter teilbar und immer einer konkreten Person zugewiesen. Ein mögliches Arbeitspaket wäre beispielsweise bei der Planung eines Events „Buchung der Musikerin für Samstagvormittag“. Je nachdem, ob Sie innerhalb des Projekts Arbeitspakete für sich selbst oder andere schreiben, ist eine detaillierte Beschreibung der zu erledigenden Aufgaben nötig oder nicht.
5 Schritte zum Projektstrukturplan mit Beispiel
Um einen Projektstrukturplan zu erstellen, sind fünf Schritte nötig:
- Wahl der Orientierung (funktionsorientiert, phasenorientiert, objektorientiert oder gemischt)
- Wahl des Schemas (Top-down, Bottom-up oder Jojo)
- Definition der einzelnen Arbeitspakete
- Verknüpfung und Zusammenführung aller Aufgaben und Teilprojekte (je nach Schema)
- Codierung des gesamten Plans
In der Praxis sieht ein Projektstrukturplan beispielsweise wie folgt aus. „AP“ ist die gängige Abkürzung für Arbeitspaket.
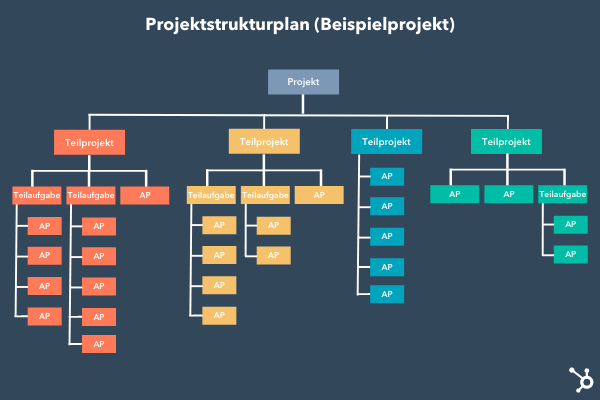
Neben dieser Baumstruktur sind auch andere Darstellungsformen wie eine Mindmap möglich.
Fazit: Ein Projektstrukturplan verbessert Ihre Organisation
Ein Projektstrukturplan hilft Ihnen bei der Erfassung aller Arbeiten, Schritte und Verantwortlichkeiten eines umfangreichen Projekts. Gleichzeitig gilt der PSP in der Praxis als Basis für weitere Pläne, beispielsweise Zeitpläne oder Ablaufdiagramme, und wird daher oft als „Plan der Pläne“ im Projektmanagement bezeichnet.
Titelbild: akinbostanci / iStock / Getty Images Plus